Traditional/Indigenous Way of Soap Production.
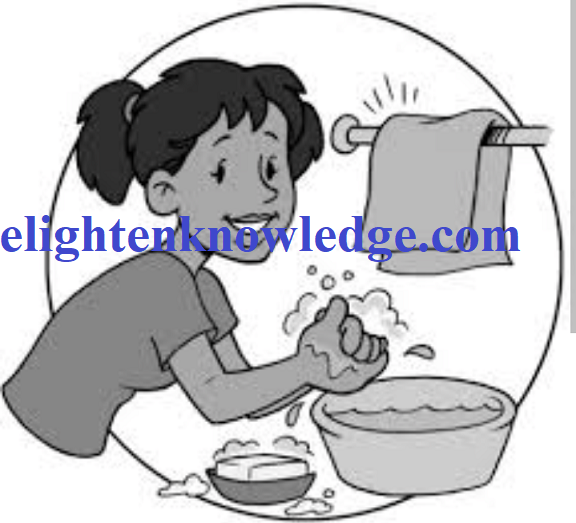
Traditional/Indigenous Way of Soap Production.
Content:
|
Introduction
In soap production, we need fat or oil and alkali as the main reactants for saponification to take place.
This is the reaction between alkali (e.g., sodium hydroxide) and oil or fat to produce soap is known as saponification.
We therefore use raw materials that will give us the alkali on one hand and the fat or oil on the other hand.
Scientific principles involved in soap production
The two main scientific processes involved in soap production are;
- Saponification.
- Decolouration.
Raw materials used in manufacturing indigenous soap.
Sources of alkali
- Ash of cocoa pods.
- Ash of plantain peels.
- Ash of coconut husks.
- Ash of palm nut husks.
Sources of fat or oil
- Palm oil.
- Palm kernel oil.
- Shea butter.
- Coconut oil.
Other raw materials are;
- Salt
- Water
Traditional soap is produced through the following stages:
- Dry cocoa pods or plantain peels are burnt into ashes.
- Water is added to the ashes obtained, stirred and filtered to obtain a solution.
- Adequate palm oil is poured into a can and heated.
- The solution is then poured into the hot palm oil.
- The water is boiled and stirred for some time.
- It is then allowed to cool.
- A concentrated salt solution (brine) is prepared and added to the mixture to precipitate the crude soap (crust).
- The crust that formed or settled on top of the liquid is removed and washed with water to remove the excess glycerol.
- The solid is pressed between filter paper and allowed to dry.
- The end product is the soap.
Ways of improving the quality of traditional (local) soap
- Avoid the use of excess alkali.
- Using well-refined or pure reactions.
- Blending oils or fats rather than the use of one type of oil or fat.
- Refining the products.
- Sorting out the products or removing excess glycerol.
- Improving upon packaging.
- Addition of colour to make it attractive.
- Addition of perfumes to improve the scent.
- Cutting into attractive shapes.
The by-product of soap production.
- Glycerol is the by-product of the saponification process (Soap production).
- Glycerol is used in the manufacturing of cellophane film, dynamite and cosmetics.
Effects of excess alkali in soap production
- The soap produced may itch the skin when it contains excess alkali.
Main stages in the modern manufacture of soap
- Saponification
- Salting out to separate the soap from the glycerol
- Repeated washing with water.
- Fitting (adding water and boiling the resulting mixture to give a uniform consistency).
- Drying
Similarities between indigenous and modern soap.
- They are made from the reaction between fat/oil and an alkali/base.
- Both types of soap lather with water.
- And also, the main reactants in both cases are fat/oil and alkali/base.
Differences between modern soaps and indigenous soaps |
|
Modern soaps | Indigenous soaps |
Does not cause itching of the skin. | May cause itching of the skin. |
Harder in texture. | Softer in texture. |
It has a pleasant odour and attractive colour. | Impurities can cause undesirable |
Contain less crude/oil and impurities. | The level of crude/oil and impurities is higher. |
Easy to mould into various shapes due to their hard texture. | Not easy to mould into shapes due to their soft texture. |
- In the industrial manufacture of soap, the aqueous solution containing glycerol is called lye.
- Soap prepared with sodium hydroxide and mainly animal fats is known as hard soap.
- But soap prepared with potassium hydroxide is known as soft soap.
Join Enlighten Knowledge WhatsApp Channel.
Join Enlighten Knowledge Telegram platform.