Seed Processing, Equipment Used, and How the Equipment Works.
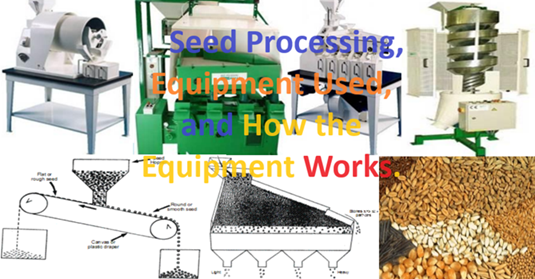
Seed lots received from the field often contain high moisture content and trash and other inert material, weed seeds, deteriorated and damaged seeds, off-size seeds, etc.
Seed processing is necessary to dry the seeds to a safe moisture level;
Remove or reduce to the extent possible the various undesirable materials, weed seeds, other crop seeds, and deteriorated or damaged seeds.
Other than this the seed lot heterogeneity in its physical characteristics like size, colour, shape, etc.
The seed lot is heterogeneous due to the following reasons;
- The soil is heterogeneous and there is a lot of variability in the fertility status of the soil due to the availability of nutrients, and physical, chemical, and biological properties.
- Variability is introduced due to the position of the seed set on the plant/fruit, time of pollination, and fertilization over some time
- Also, variability is created by biotic factors like pest and variability infestation.
- Variability is also due to the management practices like water, land preparation, levelling, staggered sowing, uneven distribution of fertilizer and irrigation water, uneven plant protection sprays, and uneven maturity at harvest.
The inherent qualities such as germinability and vigour are exemplified by certain physical characteristics of the seed i.e., large size, denser seed, optimum length, etc.,
So, if grading is done to obtain a particular range of size, shape, length, and density of the seeds, the quality of the lot is upgraded.
In its common usage, seed processing refers to all the steps necessary for the preparation of harvested seed for marketing, namely, handling, drying, shelling, preconditioning cleaning, size grading, treating and packaging, etc.
Seed Processing Plant Layout Planning
The layout plan for the construction of a seed processing plant should be carefully planned to ensure that the thorough seed cleaning, upgrading, seed treatment, and other seed processing operations are carried out efficiently, without mixing and damaging seed lots, with a minimum of equipment, personnel, time and at minimum cost.
Factors to consider in planning and designing a seed processing plant:
- Kinds of crop seeds to be handled and kinds of contaminating crop and weed seeds usually present in the seed lots
- Size of operation
- Whether drying facilities should be required
- Selection of suitable equipment
- Location of the plant
- Source of power for running machinery
- System of seed delivery to the processing plant and
- Availability of labour
The key to efficient plant layout is a thorough knowledge of what needs to be done, and sound planning.
First, the general sequence of processes involved between the time seeds enter the processing plant and the time they are cleaned, packaged, and ready for shipment, must be charted.
The sequence of operations depends upon the kind of crop and the initial quality of the seed lot, type of contaminants, moisture content of the seed lot, etc.
The layout planner must have an intimate knowledge of the seed to be processed, its physical characteristics, the contaminants in it, and also the selection of machines used to bring the seed to acceptable marketing standards.
Seed Processing Plant Building Layout
The seed processing plant building will comprise of following components:
- Receiving-cum-drying platform
- Processing area
- Auxiliary building
Receiving-cum-drying platform
- This area will be utilized to receive the raw seed and to sun dry small lots of crop seeds.
- This area can also be utilized for the storage of seeds on wooden pallets.
- The platform will be connected to the processing shed through a rolling shutter.
Processing area
- The processing area should be situated between the shed and the ventilated storage building.
- The hall should be connected to ventilated flat stores through a covered gallery for easy movement of processed and packaged seeds to seed stores.
- The hall should have a big rolling shutter in the processing plant to permit the entry of seed processing equipment into the hall for installation.
- Height will be kept to facilitate the installation of the seed processing equipment and machinery.
- A sequence of processing machines to be installed.
- Floor of the processing hall should be above the ground level.
- The shed should have sufficient provision for natural as well as forced ventilation to maintain a congenial atmosphere inside the shed.
- The shed should accommodate seed scalping, seed processing, and packaging equipment and will have sufficient space for weighing and packaging.
Auxiliary building
- In addition to the building discussed above, a provision should be made for a generator room.
- Sufficient length of road should be provided to connect various functional buildings and the main highway.
- Boundary walls should be provided all around the complex for security reasons.
- The entire complex should have a good drainage system.
- Provision for firefighting equipment such as extinguishers, water buckets, sand buckets, etc. should be made to fight minor fire hazards.
- The processing plant building should be constructed as per CPWD/PWD norms.
- It should have tubular trusses, AC sheets pitched hole roof, cement concrete flooring finished with water-proofing cement paint, aerated, ventilated, rat proof, and bird protection.
- Sealed doors should be provided in these buildings.
- Buildings will be suitably planned to have an interconnection for the movement of seeds and materials.
Analysis of Operation
-
Processing sequence:
After the machines needed have been identified, the next step is to determine the proper processing sequence.
The seed separators, elevators, conveyors, and storage bins should be so arranged that seeds flow continuously from beginning to end, and yet be flexible enough to bypass a machine or return to a part for re-cleaning.
-
Matching capacity:
Equipment size of capacity must be carefully planned to prevent bottlenecks.
When the overall operating capacity needs have been determined, all machines must be able to handle that capacity with some reserve capacity for problem lots.
Surge bins can handle variations in individual machine capacities.
But when differences are great, either larger models or more than one machine installed in parallel flow, must be used to maintain uninterrupted flow.
-
Conveying:
The type of conveying system is also a very important factor.
The conveying system must be able to handle the capacity needed in a particular spot.
And it must be carefully adapted to the seed handled.
There are three main types of processing plant layouts:
- multistorey,
- single level,
- and combination.
Multistorey:
- In this system, seed is carried by elevators to the top floor and emptied into large bins.
- Cleaning machines are then arranged in a vertical series on the lower floors.
- Seed flows from one machine down into the next by gravity.
Single level:
- In the single-storey plant, the seed is moved from one machine to the next by elevators placed between the machines.
- A great advantage of the single-level system is that one man can supervise the processing line without running up and downstairs.
- He can thus maintain closer supervision of all operations.
Combined designs:
- A compromise between the single and multistorey systems could also be adapted.
NOTE;
- After the proper machines, elevator capacities, cleaning sequences, and layout design have been selected, detailed layout planning can begin.
- Careful layout planning can identify and remedy bottlenecks and trouble spots before the plant is built, and thus prevent trouble later.
- As the layout or design develops, it should be drawn on paper.
- A good method is to draw lines of flow first and then convert these flow lines into machine lines.
- After appropriate revisions, detailed drawings can be made to show the exact locations of equipment and distances.
- Scale drawings are the most widely used method of layout planning.
- Scale models and scale templates are also very effective but are more expensive.
Requirements in seed processing
- There should be complete separation
- Minimum seed loss
- Upgrading should be possible for any particular quality
- Efficiency
- It should have only a minimum requirement
Equipment for Seed Processing
Air screen cleaner
This is the most important machine of every cleaning plant.
It uses screens and aspiration (air blow) for two separations.
A coarse upper screen removes larger material,
A lower fine screen stops the seeds and lets through fine matter
Then the seed fraction passes through a transverse or nearly vertical air stream which can separate light impurities such as empty or partly filled seeds, husks, and glumes from the seed.
In most cases, several sieves with different sized perforations are used and the cleaning is a process of gradually shifting out smaller particles.
Factors that determine the quality and quantity of seed cleaned include;
- the size of the perforations,
- the precision of the perforation,
- angle at which the sieves operate,
- the amplitude and speed of movement of the sieves,
- and correct cleaning and maintenance of the equipment.
Cleaner cum grader
The dried seeds should be cleaned and graded with the help of a cleaner cum grader.
For large-scale cleaning and grading the commonly available machine is the “Crippen Model Seed Cleaner cum Grader”.
It consists of the following parts
- A hopper in the top for seed filling
- A fluted roller below the hopper to regulate the seed flow to the screen.
- Screen (or) sieves: Perforated metal sheets with specific sizes of perforation in which there are two types.
- Rectangular perforations for paddy and
- Round perforations for seeds other than paddy
- Screen shaking unit: for oscillating the sieves to move the seeds on the screens
- Screen brushes to remove the blocked seeds
- Air blower with adjustments for air outlet
- Collecting outlet
- Air duct for directing the blown-up light particles outside
- Collecting bins.
Working principle
The seeds are fed into the hopper and they are guided to fall on the first sieve.
The first sieve is a scalping screen that scalps all the foreign materials larger and heavier than the seed and the entire quantity of seed passes through the first sieve.
The second sieve is a cleaning sieve which removes all the unwanted particles larger in size than the seed.
But the third sieve is the grading sieve which size grades the seed lot and brings it into a uniform size and also screens the undersized, shrivelled, and immature seed, dust, and dirt.
The seeds are then rolled and passed through an air column, where they are relieved of the light chaffy and other materials by the blowing air.
Types of seed cleaner cum grader
- Crippen model cleaner cum grader
- Clipper model cleaner cum grader
- Petkas cleaner cum grader
Disc separator
It consists of a series of discs, which revolve together on a horizontal shaft inside the cylindrical body.
Each disc contains many undercut pockets.
The seed enters the intake end of the separator and moves through the open centers of the discs toward the discharge end of the machine.
As the discs revolve through the seed mass the pockets lift out short seeds but reject longer seeds.
Longer seeds are conveyed by flights on the disc spokes towards the discharge end of the machine where they go out through the tailings gate.
The rate of seed travel through the open disc centers is controlled by a conveyor or blades attached to the spokes of the discs.
The disc separator makes a very precise separation.
No factor other than seed length and shape affects its separation.
Flexibility is obtained by varying size of the pockets.
Indented cylinder separator
The indented cylinder separator is a rotating, almost horizontal cylinder with movable, horizontal separating adjustments that are mounted inside it.
Indent lines are there inside the surface of the cylinder.
The indented cylinder revolves, turning the seed mass to give each seed a chance to fit into the indent.
Short seeds are lifted out of the seed mass and are dropped into the lifting and long seeds remain in the cylinder and are discharged out via., a separate spout at the end of the cylinder.
As the cylinder revolves, it creates centrifugal force which helps to hold the seed in the indent.
Short seeds are held in the indent until the cylinder turns to the point where the indent is inverted enough for gravity to cause the seed to fall out of the indent.
The length, surface texture, and size of seeds determine how they fit into the indent so that they can be lifted out of the seed mass.
The speed of the cylinder creates centrifugal force which holds the seeds in the indent as they are lifted upward.
Thus, the shape and size of the seed cause some seeds to fall out after being lifted only a short distance, while other seeds are lifted closer to the top of the cylinder before they fall out.
As the seeds enter the cylinder, the small, short, easy-to-separate seeds are quickly removed.
The center cylinder section removes the intermediate sizes of seeds still in the cylinder.
All indents in a cylinder are the same size, only the progressively declining amount of material to be lifted causes this difference in separating action.
Adjustments
- Cylinder speed
- Size of the indent
- Trough setting
- Tilt of the cylinder
- Adjustable retarder.
Specific gravity separator
Seeds of the same size and general shape can often be separated because they differ in specific gravity or relative weight.
This difference is very useful in removing light, immature seeds or heavy sand and rocks to improve the purity and germination of crop seeds.
If seeds that differ in specific gravity (relative weight/unit of volume) are placed on a substrate of intermediate density, seeds of higher specific gravity will fall through the substrata, while seeds of lower specific gravity will be buoyed up the substrata.
Here air is used as separation substrata.
Working principle
As seeds flow on the deck of the gravity separator, they enter a column of air coming up through the porous surface of the deck.
The pressure of terminal velocity of the air rising through the deck can be controlled very closely to separate two kinds of seeds differing in specific gravity, the air is adjusted so that only the lighter seeds are lifted off the deck surface.
These lighter seeds are held up by air pressure and tend to float on the deck surface.
The heavier seed possess a velocity greater than that of the air columns so they are not lifted and so will lie on the deck surface.
The air column thus stratifies the seed mixture into vertical zones of relative weight with the heavier seed lying on the deck and the lighter seeds lifted to the top of the seed mass.
Adjustments
- Feed rate
- Airflow
- End slope
- Side slope
- Deck oscillation speed
- Deck speed.
Roll mill/dodder mill/velvet roll mill
It is used to separate the seeds based on surface texture and shape.
This separator should be used only after the seed has been carefully cleaned and separated from the chaff.
These are effective in separating seeds with a rough seed coat or shape angles from smooth seeds.
Working principle of the rolling mill
The rolling mill consists basically of two rollers, covered with flannel or velvet, placed side by side so that they touch each other down their entire length.
The rollers are mounted on an incline and they turn in opposite directions.
A curved adjustable shield is mounted above the rollers.
The mixture of smooth and rough seeds is fed into the place, where the rollers touch each other, at the high end of the machine.
As the rollers turn up and out, seeds that are rough or have sharp or broken edges are caught by the nap of the fabric covering the rollers.
These seeds are thrown up against the curved shield.
They strike the shield at an angle, bounce back down to the roller, and are again thrown up against the shield.
Smooth seeds bounce down the inclined position forward between the rollers, and discharge at the lower end of the machine.
They are not affected by the fabric roller covering and are not pitched over the side of the rollers.
Adjustments
- Rate of feed
- Speed
- Clearance between shield and rolls
- The angle of inclination of rolls.
Magnetic separator
The separation is mainly based on the affinity for liquids which is used for separation.
Since seeds contain no free iron and are not attracted by a magnet they must be selectively pretreated with a magnetic material such as finely ground iron powder.
Rough seed coats, cracked or broken seed coats, dirt lumps, chaff, or seeds with a sticky residue on the surface will hold the liquid and become sticky so that iron powder will adhere to them.
Smooth-coated seeds will not absorb liquid.
So, no iron powder will adhere to them.
The seeds are then discharged from the mixing chamber and brought into contact with a powerful magnet, which removes the iron-coated seeds.
Most magnetic cleavers pass the seeds over a revolving drum which has a high-intensity magnetic field.
Seeds with an affinity for liquids which are now coated with iron powder are attracted by the magnet and adhere to the drum until they are removed by a brush or scraper.
Seeds that are relatively free of iron powder are not attracted by the magnet and will fall into a separate discharge spout.
The first requisite of magnetic seed separation is that the seed to be separated must possess different seed coat characters.
Crop seeds should have a smooth surface, while the seeds to be removed should have a rough surface that will retain liquid and can accept the iron powder.
Success in separating the components depends upon the magnitude of seed coat differences and the thoroughness with which the moistened seeds and the iron powder are blended.
Colour separator
Many large crop seeds such as peas and beans differ in colour between varieties.
Colour variation may also occur due to immaturity or disease.
Electronic colour sorting machines can separate such seeds by the difference in colour and also remove mud balls and discoloured seeds in the same operation.
The electronic colour sorter views each seed individually with photoelectric cells.
The seed is compared with a selected background or colour range and is discharged from the machine according to its colour.
If it is the great desired colour, the seed is discharged through the good seed spout.
If its colour or shade falls within the reject range, a blast of compressed air deflects the seed and sends it into the reject discharge spout.
These are highly sensitive. Since the machine views each seed individually, capacity is low, but the initial cost is high and the operating cost is less.
The usefulness of the machine is greater with large seeded crops.
Spiral separator
The separator, which classifies seed according to its shape and rolling ability, consists of sheet metal strips fitted around a central axis in the form of a spiral.
The unit resembles an open screw conveyor standing in a vertical position.
The seed is introduced at the top of the inner spiral.
Round seeds roll faster down the incline than flat or irregularly shaped seeds, which tend to slide or tumble.
The orbit of the round seed increases with speed on its flight around the axis,
Until it rolls over the edge of the inner flight into the outer flight where it is collected separately.
The slower-moving seed does not build up enough speed to escape from the inner flight.
Most spirals have multiple inner flights arranged one above the other to increase the capacity.