Methods and the Techniques Used in Seed Drying After Harvest
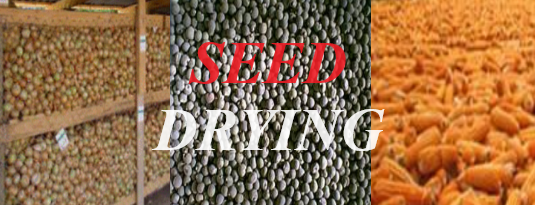
Methods and the Techniques Used in Seed Drying After Harvest
The process of elimination of moisture from the seed is called drying.
Seed drying should reduce the seed moisture content to safe moisture limits to maintain its viability and vigour during storage;
Which may otherwise deteriorate quickly owing to mold growth, heating, and enhanced microbial activity.
Seed drying also permits early harvesting, long-term storage of seeds, more efficient use of land and manpower, the use of plant stalks as green fodder, and the production of high-quality seed.
Depending upon the climate and method of harvesting adopted the threshed seed may or may not be dry enough for safe storage.
Under less favourable conditions, the threshed seed needs further drying.
Stage of moisture elimination
The moisture from the seed is eliminated in 2 stages
- The surface moisture of the seed that was initially removed by the drying air.
- The removal of the moisture in the surface causes an imbalance in the moisture potential in the surface of the seed and the inner portion of the seed which leads to the migration of moisture from the inner organ to the surface.
The migration of moisture to the surface is slower than the evaporation and a moisture gradient is developed in the kernel.
Elimination of moisture from the seed depends upon the relative humidity and temperature of the environment surrounding the seed.
When the RH of the atmosphere is less than the seed, moisture is eliminated from the seed.
While drying, care should be taken to minimize /prevent oxidation decomposition, and volatilization.
In this process, there will be a loss of dry weight of seed which is widened when the processes take place at high temperature.
Hence, high-moisture seeds should be dried at low temperatures.
Equilibrium moisture content
A seed is in equilibrium with the environment when the rate of moisture loss from the seed to the surrounding atmosphere is equal to the rate of moisture gained by the seed from the atmosphere.
The rate of drying depends on;
- Initial seed moisture content
- Size of the bin and capacity
- Depth of spread of seed
- The rate of air blow
- Atmosphere air temperature and relative humidity
- Static pressure
- Drying temperature
Methods of drying
- Physical drying (or) natural drying (or) traditional sun drying
- Mechanical (or) artificial drying
- Drying with forced natural air
- Drying with forced artificially heated air
- Drying with desiccants
- Drying with infrared rays
Physical drying /Natural drying /Traditional Sun drying
This is the common conventional method in which drying of the harvested crop is carried out in the field or threshing floor by the radiant energy of the sun.
This does not involve any expenditure. To achieve uniform drying, the seed should be spread in a thin layer.
High moisture content seeds with a moisture content of more than 17% should be dried first under shade/light to reduce the moisture content to less than 17% and then dried under heavy sun i.e. noon drying.
Sun-dried seeds should not be allowed to remain open on the floor during the night since seeds will absorb moisture from the air. 2-4 days are needed to reduce the moisture content to 10-12%.
Direct sunlight also can adversely affect seed germinability owing to high temperature and ultraviolet radiation, especially if the moisture content of the seed is high.
Advantages
- Easy and cheap
- Does not require any expenditure or fuel.
Disadvantages
- The rate of drying is slow
- Loss due to attack by insects, birds, and animals
- A large floor area is required
- Involves extra labour for collecting and exposing during the day
- Sun drying causes sun checks or hot spots due to variations in temperature from time to time. These checks or spots induce a high amount of breakage while processing
- Mechanical mixtures are possible
- Dust, dirt, and other foreign materials get admixed
- High weather risks and damage by heavy wind and rains
Mechanical drying or artificial drying
-
Forced air drying
In forced air drying, natural air or air supplemented with heat is blown through a layer of seed until drying is completed.
Generally, ordinary seeds are provided with two types of ventilators for free movement of air circulation.
In modern times, provisions are to be made for the forcible circulation of air with the help of an electronic blower.
The outside air which is comparatively dry is circulated and thereby the seed gets dried up in this process.
This is possible only in dry months.
Two types of driers are used:
- batch driers
- and continuous flow driers.
Batch driers
In batch drier, relatively dry air is blown through a seed layer until the seed is dried completely, after which it is removed and replaced by another batch of seed.
The method is simple and well suited to small quantities of seed, allows easy cleaning, and is recommended for farm drying.
In horizontal drier, the seed is contained in a box or chamber with a perforated floor through which the air is blown.
Air ducts can be installed on a barn floor and the seed to be dried and piled over them.
In a modified sack drier, seed contained in a woven sack is placed on a grid through which air is blown.
A cylindrical storage bin with a raised perforated floor arranged to blow air underneath the floor can also be used.
A vertical batch drier consists of two concentric perforated cylinders.
The space between the two cylinders is filled with seed and air is blown into the inner cylinder from where it passes outward the seed.
The size of the batch determines the drying rate.
In the horizontal batch drier, the seed at the bottom dries first, with the dry zone extending gradually upward.
The drying of the uppermost seed may be delayed unduly if the seed layer is too thick or the airflow is inadequate.
The seed layer should not exceed a depth of 3m and for high moisture forage seed, it should be reduced to 1m or less.
If the seed is dried in a storage bin, a layer of undried seed can be added on top of the dried batch and drying continues, but only if the seed is already fairly dry and air is not too hot.
Seed loss also can be avoided by drying in two stages.
After the first batch has partially dried, the emerging air is passed through a second batch held in another chamber, repeating the process with the second batch and so on.
The air blown through a batch must not be too hot, because the seed at the bottom may be overheated by direct exposure to the entering hot air.
It is often not necessary to heat the air at all, and heating to less than 10o C above the ambient temperature can be very effective,
But on a hot humid day in the tropics, even a few degrees above ambient temperature can harm the seeds.
Dehumidifiers may need to be used under these circumstances.
An appropriate drying rate is very important.
Too rapid drying may harm the seed because of the high drying temperature or a quick water loss from the seed.
Slow drying may mean maintaining a high moisture seed at a higher temperature for a prolonged time, resulting in the deterioration of the seed.
Continuous flow dryers
In this type of drier, the seed moves horizontally or vertically through a stream of hot air and then into a cooling chamber. These driers are however difficult to clean when there is a change of cultivar. These driers can use air temperatures higher than those of batch dries, because the seed is heated for a much shorter time.
-
L.S.U. dryers (Louisiana State University dryers)
This is a continuous column heated air drier largely used for paddy.
The paddy seeds are fed from the top with the help of gravity force in a zig-zag manner and heated air is blown from the bottom usually at right angles to the direction of seed motion.
The falling seeds get dried up by the heated air and this process is repeated till to get a reduction of moisture content to the expected level.
-
Non-mixing column dryer
These dryers consist of a tall vertical column through which paddy flows by gravity.
No provision is made for agitating the paddy as it flows and hence there is no attempt to drive the paddy from a straight path.
Paddy descends gradually between two parallel screens and heated air is forced through the screens.
Advantages of bin dryers
- Short drying period
- Less damage or spoilage during wet weather
- Drying is more uniform.
Advantages of mechanical drying
- Quick method, timely, and uniform drying is possible
- Making early harvest possible
- It reduces the chances of losses due to over-ripening and shattering of seed
- Losses due to rodents and birds are prevented.
- Less damage during the processing operation.
- Permits long-term storage by preventing sun checks and other damages.
Disadvantages of mechanical drying
- The initial cost of drying the equipment is high
- Fuel is expensive
- It produces possible fire hazards
- Considerable supervision is necessary.
Storage structures for Seed drying
Building requirements for a seed drying system depend upon the size of the operation, the number of different seeds to be dried, the level of mechanization desired, and future expansion.
Different types and forms of storage structures can be built for handling seeds to be dried with forced air.
These may be made of steel, wood, plywood, or concrete and they may be cylindrical or rectangular.
Regardless of the type of structure, all storage bins used for forced air drying in the storage of seeds must have the following features.
- Small grain seeds in bulk exert large pressures against the sidewalls. The side pressures are converted to a vertical load on the foundation, which should be strong enough to hold the seed lots.
- The roof and walls of bins must be airtight for drying to proceed satisfactorily.
- The openings for filling and removal of seeds should be large and convenient to use. A full-size entrance door is desirable.
- A hand space of about 1 m should be provided for easy inspection of the seed. Cleaning and spraying operations should be convenient. For fumigation, the structures should be airtight, with a provision for temporary sealing of all openings.
- The structure should be able to dry and store more than one kind of seed.
- The drying air should be uniformly distributed through all portions of the seed lot for efficient drying.
- The flow of air leaving the seed should proceed rapidly so that back pressures do not hinder the flow of drying into the seed.
Air-Distribution Systems
Three types of air-distribution systems are used for seed drying.
- The main and lateral duct system
- a single central perforated duct
- and the perforated false floor system.
Multiple bin storage structures for drying can be built so that they are arranged to enable the drying of several seed lots simultaneously using the same drying fans.
Alternatively, different seed lots can be dried successively with sliding air gates controlling the flow of air to the respective bins.
A multiple-bin arrangement is particularly useful for drying more than one kind of seed simultaneously.
Heated air-drying system
Heated air driers consist of;
- A heater unit where fuel is burned and
- A fan forces the heated air through a canvas connecting duct into the air distribution system of the drying bin.
- Safety features such as automatic thermostatic high limit temperature control, which cuts off the burner flame if the air temperature exceeds a certain safe maximum, and flame failure control, which automatically cuts off fuel flow to the burner if the flame goes out are provided.
- A thermostat can also automatically maintain the air temperature at a desired setting
- In many driers, such thermostats are provided as a standard feature.
Two main types of driers are available, which differ in the manner heat is supplied to the air.
- Direct fired
- And indirect fired.
In a direct-fired drier;
- The fuel is burned and the hot combustion gases are thrown directly into the air distribution system.
- Although the heat is used very efficiently, there is the possibility of blowing soot, unburned fuel, and objectionable fumes into the seed.
- The burner, therefore, needs to be adjusted properly to burn the fuel completely.
- With certain fuels, there is also a danger of blowing small sparks into the seed.
In indirect-fired driers;
- The hot combustion gases pass into a chamber.
- The drying air circulates this chamber and picks up heat as in a hot air furnace.
- The drying air thus does not include combustion gases, sparks, soot, or fumes.
- These driers are less efficient in the use of heat but are safer than direct-fired types.
The driers are designed to burn various types of fuels (e.g. liquid propane or butane, natural gas, fuel oil, and coal.
Both liquid propane and natural gas burn readily with minimum soot and are the best fuels for direct driers and kerosene oil is better for indirect fired driers.
Two important aspects that must be considered while calculating the requirements of a suitable crop drier are the required airflow volume and the heat capacity (BTU/hr) for drying seeds at the specified desired rate.
The fan requirements can be computed by knowing the total airflow at the static pressure of the seed at a given drying depth and heater requirements are estimated by calculating the amount of water to be removed from the seed per hour.
Based on these calculations, a suitable crop drier can be selected to provide a minimum required airflow volume (bin capacity x air flow rate) and heat capacity in BTU/hr.
Types of heated driers
- layer-in-bin,
- batch-in-bin,
- batch,
- and continuous driers
Stirring devices keep the seed in a loose fill condition, allowing easy airflow through the bottom layers.
Such mechanisms alleviate the problems of uneven drying (or over-drying) by breaking up pockets of fires and trash and blending the seed by constant mixing.
Large differences in the degree of drying between the top and bottom layers of the seed have been noticed during drying by heated air.
It is, therefore, advisable to dry seed at shallow depths to minimize these differences and avoid overheating of the bottom layer.
According to Agrawal, maximum seed depths and temperatures for batch drying of seeds of different crop species are in bins.
Heated air drying requires higher rates of airflow because water is evaporated faster and more air is needed to carry it away.
The higher airflow rate also ensures more uniform drying of the top and bottom layers of the seed, completing the drying much faster at the recommended temperatures.
The general procedure for bin drying of seeds with heated air consists of changing the seed into the bin to the recommended depth.
The drier is operated at the recommended temperature of the seed using either manual or thermostatic controls to set the desired temperature.
After drying is completed, blowing of the air through the seed is continued for some time without heat to bring the seed to an ambient temperature.
Some variations of batch drying with heated air include;
- wagon drying,
- bag drying,
- and box drying.
Wagon drying,
In wagon drying, the seed is loaded directly onto a wagon especially constructed for drying.
The wagon is then drawn to the drier unit and connected with a canvas distribution duct.
Forcing the air up through the perforations in the wagon floor dries the seed.
After drying, the wagon is disconnected from the canvas duct, and the seed is cooled with a fan towed to the storage bins.
Wagon drying provides;
- continuous drying,
- versatility,
- easy cleaning,
- and low initial cost.
Bag drying,
Bag drying is another suitable variation to handle several varieties of smaller quantities of seed simultaneously.
Seed received in jute bags is exposed to airflow with minimum static pressure because the drying bed is only one sack deep.
Typical design criteria provide 25 – 40m3 of air/min/m3 seed at a static pressure of 3cm less.
The construction is simple and inexpensive.
Box drying
A box drier is a modified bag drier well adapted to dry smaller quantities of basic or foundation seed.
With box driers, it is possible to maintain the identity of small seed lots despite handling.
The boxes can be constructed of locally available materials, which are fitted with perforated metal or woven wire bottoms.
NB:
- Seed is usually dried in stages with heated air each stage consisting of a pass through the drier.
- Between passes the seed is stored in bins for an equilibrium period known as a tempering period.
- This period of tempering shortens the total drying time.
- During drying, surface moisture is removed and internal moisture moves towards the surface slower than evaporation, and a moisture gradient develops in the kernel.
- The outside becomes drier than the inside and the evaporation rate decreases.
- During tempering moisture concentration equalizes in the kernel and then evaporation of surface moisture is nearly as rapid as at the start of drying.