How to Processed Seeds for Storage and the types of equipment used in Seed Treatments
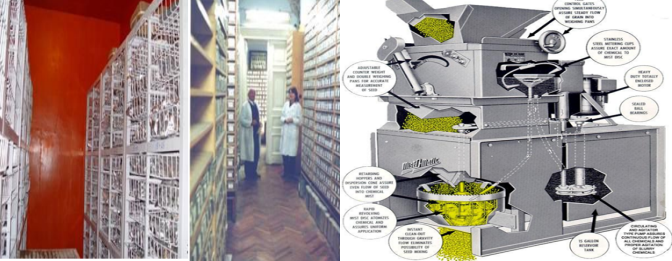
How to Processed Seeds for Storage and the types of equipment used in Seed Treatments
Pre-storage treatments of seeds.
Pre-storage treatments of harvest-fresh seed are primarily aimed towards protection against deteriorated senescence during storage.
Seed storage which is again threatened by insect and pathogen attack, can also be taken care of by prescribed pre-storage seed treatments.
- Halogenation
- Antioxidant treatment
- Seed sanitation
Mid-storage treatments
Seeds in storage accumulate damage to cell membranes during senescence.
Mid-storage seed treatments are capable of reducing the age-induced damages and restoring the seed vigour to a certain extent besides, the seed viability and productivity of stored seeds are also improved.
-
Hydration–Dehydration
It is the process of soaking the low and medium vigour seeds in water with or without added chemicals usually for short durations to raise the seed moisture content to 25–30% and drying back the seeds to safe limits for dry storage.
The hydration–dehydration treatments
- Should be given only to stored seeds.
- Is effective in low and medium vigour non-leguminous seeds,
- The moisture equilibration and moist sand conditioning treatments in which moisture is taken up by the seed slowly and progressively, are recommended for relatively high- vigour seeds and seeds of pulses and leguminous vegetable crops
- Direct soaking of leguminous seeds should be avoided.
- Would not make a seed germinable, which has already lost viability.
Types of H-D treatments
The wet treatments include soaking-drying, dipping-drying, spraying-drying, stepwise hydration-drying, moisture equilibration-drying, moisture equilibration soaking-drying, moist and conditioning-drying, etc.
The choice of treatment depends upon the characteristics of the seed and the initial vigour status of the seeds.
Soaking–Drying
Stored seed is soaked in water or a solution of chemicals sufficient to cover it and kept at room temperature for 2-6 hours depending on the material with occasional stirring.
The soaked seed is taken out and after surface drying in the shade for some time, dried back to the original moisture content
Dilute solution of chemicals such as sodium or potassium phosphate (di and mono basic), sodium chloride, p-hydroxy benzoic acid, p-amino benzoic acid, oxalic acid, potassium iodide, etc can also be used at 10-4 to 10-3 M concentrations.
Fungicidal and insecticidal formulations can also be incorporated in the soak water.
Dipping–Drying
Seeds are dipped in water or solutions of the aforesaid chemicals for only 2-5 minutes and the wet seed is taken out immediately and kept covered for 2 – 6 hours depending on the material, for absorption of surface water followed by drying back in S-D.
This treatment is effective in most high and high-medium vigour seeds of rice, wheat, jute, summer and winter vegetables
Spraying–Drying
Seeds are spread in a thin layer and then an amount of water (approximately 1/5 to ¼ of the seed weight) is sprayed onto it in two equal installments (turning over the seed layer after the first spray) and then kept covered by a polythene sheet for 2-4 hours before drying back.
This treatment is similar to D-D in its efficacy and suitability.
Moisture equilibration–drying (ME–D)
Here, the seeds are placed in thin layers on trays kept on a raised platform in a closed moisture-saturated chamber lined internally with moist blotters giving nearly 100% RH at room temperature.
After 24-48 hours, depending on the material and ambient temperature, the seed is dried back in the usual way.
For soaking injury-prone seeds this treatment, which gives a slow and progressive rise in moisture content, is very effective.
ME-D, however, is difficult to practice on a large scale and is not advocated for low vigour non-leguminous seeds because of the possible aging effect of the treatment especially when given for prolonged periods.
Moist sand conditioning–drying (MSC-D)
This treatment is similar to the moisture equilibration treatment but easier to practice.
For slow and progressive moisture uptake, the seed is thoroughly mixed with pre-moistened sand, using 3 times the amount of air sand than the seed.
The moisture content of sand is adjusted to 5- 10 by adding the requisite amount of water or solution of chemicals to previously washed and dried fine grain building grade sand.
The addition of water should be so adjusted as to get the required hydration effect without initiating the germination process.
After mixing the dry seed with the premoistened sand, the mixture is kept at room temperature for 16–36 hours depending on the material and sand moisture content.
The seed absorbs moisture from the sand and after incubation, the hydrated seed is separated from sand by sieving and dried back to the original weight.
Mode of Action The main purpose of hydration is to raise the seed moisture content to 25–30% (wet weight basis) before drying back to safe limits for dry storage.
The hydration-dehydration treatment may improve the vigour by controlling free radical reactions and consequent peroxidative damage to lipoprotein cell membranes.
SEED TREATING EQUIPMENT
Commercial seed treaters are designed to apply accurately measured quantities of pesticides to a given weight of seed.
There are three types of commercial seed treaters on the market: dust treaters, slurry treaters, and direct treaters Panogen and Mist-O-Matic treaters are examples of direct treaters.
Dust Treater (Gustafson XL Dry Powder Seed Treater)
-
Controlling the Flow of Seed:
The number of seed that flows into the weighing pan (which is just beneath the feed hopper on top of the treater) is controlled by opening or closing the gates of the feed hopper using the hand wheel on the side of the hopper.
The scale on the hopper shows how far the gates are open (in inches).
Gates should be open to whatever number of inches it takes to keep the weighing pan filled to the required number of pounds per dump as it tilts in either direction.
The number of pounds per dump is adjusted by correctly setting the counterweight up or down on the counterweight arm.
-
Powder Application:
To be sure that the correct amount of powder is being applied to the seed flow, a preliminary test must be made in which a given number of pounds of seed (such as 100 lbs) is run through the feeder.
During this run, the measuring cup provided with the feeder should be used to catch the powder as it comes off the vibrator.
After the given number of seeds has run through, the powder should be weighed to determine how much is being applied to that number of seeds.
The vibrator speed can then be adjusted accordingly.
Then a second or more tests should be run until the proper setting of the vibrator speed is determined for correct coverage.
Slurry Seed Treater
The slurry treatment principle involves the suspension of wettable powder treatment material in water.
The treatment material applied as a slurry is accurately metered through a simple mechanism composed of a slurry cup and seed dump pan.
The cup introduces a given amount of slurry with each dump of seed into a mixing chamber where they are blended.
While the operation of the slurry treater is relatively simple, the various operation procedures must be thoroughly understood.
- The metering principle is the same indirect, ready-mix, or fully automatic treaters-i.e., the introduction of a fixed amount of slurry to a given weight of seed.
- To obtain a given dump weight, slurry treaters are equipped with a seed gate that controls seed flow to the dump pan. With the proper seed gate setting, a constant dump weight for a given can be obtained.
- The amount of treatment material applied is adjusted by the slurry concentration and the size of the slurry cup or bucket. As the dump pan fills, a point is reached where it over-balances the counterweight and dumps into the mixing chamber. This brings the alternate weighing pan in position to receive the inflow of seed and activates a mechanism to add a cup of slurry to the mixing chamber. Thus, one cup of slurry is added with each dump of seed.
- The mixing chamber is fitted with an auger-type agitator that mixes and moves seed to the bagging end of the chamber. The speed of the auger is important because at slow speeds more uniform distribution is obtained.
NB:
Slurry tanks have 15 to 35-gallon capacities, depending upon the size of the treater.
They are equipped with agitators that mix the slurry in the tank and keep it suspended during operation.
The powder must be thoroughly suspended in water before treatment.
If the treater has been idle for any period, sediment in the bottom of the slurry cups must be cleaned out.
The proper size slurry cup must be used.
Most machines now have cups with ports and rubber plugs for 15 cc, 23 cc, and 46 cc quantities.
Some users prefer to mix the slurry in an auxiliary tank and then transfer it to the slurry chamber as needed.
DIRECT TREATERS
Direct treaters are the most recent development and include the Panogen and Mist-O-Matic treaters.
These two were initially designed to apply undiluted liquid treatment. Instead of applying 23 cc of material per 10 pounds of wheat, as in slurry treaters, they apply 14 to 21 cc (1/2 to 3/4 ounces) per bushel of “wheat.
This small quantity of material is suitable only with liquid materials which are somewhat volatile and do not require complete, uniform coverage for effective action.
Later modifications for direct treaters include dual tanks that permit simultaneous addition of a fungicide and an insecticide and adaptations for the application of slurries.
The metering device used in both types of direct treaters is similar to that of the slurry treater since it is attained through the synchronization of a treatment cup and seed dump.
Otherwise, the two direct treaters differ decidedly from the slurry treater and each other.
Both of these direct treaters have an adjustable dump pan counterweight to adjust the weight of the seed dump.
This is not practical with slurry treaters.
-
Panogen Seed treater
The operation of the Panogen treater is relatively simple.
A small treatment cup, operating from a rocker’s arm directly off the seed dump pan and out of a small reservoir, meters one cup of treatment with each dump of the seed pan.
Fungicide flows through a tube to the head of the revolving drum seed mixing chamber.
It flows in with seed from the dumping pan and is distributed over the seed by the rubbing action of the seed passing through the revolving drum.
The desired treating rate is obtained by the size of the treatment cup and by adjusting the seed dump weight.
Treatment cup sizes are designated by treating rate in ounces and not by actual size-e.g., the 3/4ounce cup applies 3/4 ounce (22.5 cc) of treatment per bushel with six dumps per bushel.
The actual size of this cup is approximately 3.75cc.
-
Mist-O-Matic Seed Treater:
The “Mist-o-Matic” treater applies treatment as a mist directly to the seed.
The metering operation of the treatment cups and seed dump is similar to that of the “Panogen” treater.
Cup sizes are designated by the number of cc’s they actually deliver-e.g., 2 ½, 5, 10, 20 and 40.
The treater is equipped with a large treatment tank, a pump, and a return that maintains the level in the small reservoir from which the treatment cups are fed.
After metering, the treatment material flows to a rapidly revolving, fluted disc mounted under a seed-spreading cone.
The disc brakes droplets of the treatment solution into a fine mist and sprays it outward to coat seed falling over the cone through the treating chamber.
Just below the seed dump are two adjustable retarders designed to give a continuous flow of seed over the cone between seed dumps.
This is important since there is a continuous misting of material from the revolving disc.
The desired treating rate is obtained through selection of treatment cup size and proper adjustment of the seed dump weight.